Road Cracks Sealing Robot
To all fellow drivers/passengers, have you ever been stuck in a traffic jam so long that your bottom aches, you nearly concussed from Carbon Monoxide inhalation or you wish you had some magic to shrink all the other cars and roll over them? And the traffic jam was due to a lane closure for road repair, which lasted a few days. If the road was not repaired, then there might be no road to repair!
Well, Advanced Highway Maintenance and Construction Technology(AHMCT) has the solution to those very annoying road repairs lasting a whole day. But before that, I shall state the perils of road repairs.
Everyday, workers lay their lives on the road by manually repairing the cracked road, seperated by less than 1.5m between traffic speeding at 90kmh (sometimes much higher). All it needs is a moment of distraction, or a drunked driver, to claim that life. And it is not only for a day. Manual road repairs require a lot of time, and may drag on a few days for the same stretch of highway. More time spent on road = more chance of workers hit by speeding cars.
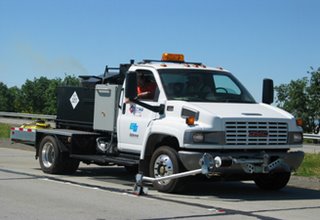
Enter the
Transfer Tank Longitudinal Sealer (TTLS). -->
This is an evolved version of the Longitudinal Crack Sealing Machine (LCSM). (Below)

This machine consists of a long robotic arm equipped with visual sensors, which sends information to the driver. The operator can then, from the comfort and safety (and aircon) of his seat, communicate with the machine through a simple user interface. The operator just needs to position the arm over a crack on the road, and the machine will take care of the rest. The arm will then take over, tracing and sealing the fissure on its own while the driver drives alongside it, monitoring the activity from the safe confines of a large truck.
Another machine is the Operator Controlled Crack Sealing Machine (OCCSM).
How It Works:
Sealing
A special sealant applicator that deploys a pressurized reservoir is developed to allow for high speed sealing operations and automation. This means, a reservoir of sealant is place over the crack, and then pressure is applied to ensure that the sealant moves to fill up the crack. Since the sealant reservoir must be kept at a constant level (so as to fill up the crack regardless of the crack depth and width), the sealant pump output is regulated with a reservoir level feedback controller constantly maintaining the set reservoir level regardless of crack demand. This application technique has proved to be successful, completely filling up cracks at a speed of 8km/h.
Vision System
As stated, there were visual sensors on the robotic arm. This provides real-time images of the workspace for crack detection and path planning. The images are routed to the operator, where he will be able to get them by simply opening a browser (not unlike your internet browser).
Motion and I/O Control System
The motion control system handles the two-axis (R-θ) motion of the telescopic arm. This node of the distributed control network is a stand-alone 2-axis motion controller with a built-in 100 Mbps fast Ethernet port. The I/O subsystem controls the pump of the sealent melter, the heaters, and the sealent head lever. It is also a stand-alone controller with 100Mbps ethernet port. Unlike the motion controller which can store and execute customer programs, the I/O controller uses a memory map for customizing temperature alarms and events which are used to control the heaters, and customizing a PID loop to control the pump proportional to the head level. All these critical tasks are conducted by the controller and real-time is ensured.
User Interface
Programmed in Visual C++, the user interface can be run on any PC, provided ethernet/Wi-Fi connection is available. The software is developed such that it is object-oriented and multithreaded, which makes the graphical interface rich in features (required by complex systems such as this), and always responsive (important for real-time control). This user interface allows the operator to perform all controls to the machine.
Path Planning
The graphical interface makes path planning interactive and allows many other functions. The operator can choose from a whole list of methods for finding the path. He can even combine the methods, and such flexibility allows the him to find the path for virtually any crack, effectively and accurately. Since fully automated crack recognition is time-consuming and not dependable, the operator can interfere and point out the start and end of the crack, avoiding the necessity to scan the whole image. A C++ program makes use of this to find the entire crack, only the start and end points of the cracks are needed as inputs. Raw paths from free hand and some other planning methods are normally not smooth which can result in jerky motions by the telescopic arm (for sealing). These jerky motions will lead to rough seals. The system encompasses curve fitting to smoothen out the edges. Nice.
Control Panel
The control panel is a modeless dialog box, meaning it is always on screen, but permits other user activites on the main window. Because of this, the operator can control and monitor the system within the control panel and do other things such as path planning within the main window. The entire user interface is always unblocked (top of screen), so the operator always has control of the system. This is very important for real-time control programming. In cases of emergencies, it is of utmost importance that the operation can be stopped immediately, especially when the machine is working adjacent to traffic.
Conclusion
The implementation of the cracks sealing robots has proved beneficial. I don't think such technology is in use in Singapore yet. However, from the statistics, this will prove much more efficient and cheaper (and less annoyance to road users) in the long run.
Statistics: (LCSM vs Manual)
No of employees: 3(LCSM), 4(Manual)
Avg miles/day: 3.5(LCSM), 0.8(Manual)
Bare Rate Cost: $4017(LCSM), $23820(Manual)
Road Closures: No(LCSM), Yes(Manual)
Employees on foot?: No(LCSM), Yes(Manual)
I hope someone from LTA reads this and use this wonderful system to alleviate the sufferings of motorists. Haha. Save $$, Save Time, Save Lives. How wonderful is that!
References:
http://www.ahmct.ucdavis.edu/index.htm?pg=HomePage
http://www.its.berkeley.edu/itsreview/ITSReviewonline/spring2003/trb2003/bennett.pdf