In future a traffic jam can be more than just time-consuming ...
We all know the situation. The flow of traffic is becoming slower, jamming and after a (long) while you can see the reason for your delay. Several signs and traffic cones are blocking at least one of the lanes, since an accident happened or the road is is beeing repaired.
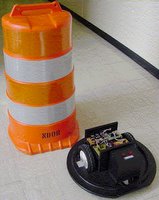
To accelerate this process, minimize the working zone, increase the safety of every road user and save money (in terms of lost productivity) Dr. Shane Farritor and his team from the Mechanical Engineering Department at the University of Nebraska-Lincoln animated the normally lifeless safety barrels (brightly colored, 130cm high, 50cm in diameter) as the first elements of a team of Robotic Safety Markers (RSM) that will include signs, cones and possibly barricades and arrestors.
Each of these Robotic Safety Barrels (RSB) has two wheels which are independently driven by two motors. Such a system of barrels consists of a lead robot and the deployed RSMs. The lead robot, which can be a maintenance vehicle, is equipped with sensors and complex computational and communication resources to globally locate and control the RSBs (deliberative control). It locates them using a laser range finder and identifies them with help of a Hough transformation algorithm.
To set the barrel’s positions the user (in the maintenance vehicle) places them by clicking on the locations in a video image of the roadway. Since normal roadways are relatively easy to predict, the primary obstacles for the RSBs are other barrels.
To calculate the desired paths, a parabolic polynomial is used to compute the waypoints for the RSBs, which are sent to them. From this moment on the barrels try to find their way to this waypoint (reactive control).
This is done by an microcontroller, running with a realtime operating system (µC/OS-II) and a PID-Controller which uses kinematic relationships between wheel velocities and coordinates to calculate path-corrections.
An example can be found in [2].
The first tests with 5 Barrels were succesful and the maximum deviation from the path and final positions was within the requirements for barrel placement and even exceeded the accuracy of current human deployment. Eventually it is probably just a matter of time until we can see this new invention on our streets.
References:
[1]http://robots.unl.edu/projects/index.html
[2]http://robots.unl.edu/files/papers2/IEEE_Intelligent_Systems_Nov.Dec2004.pdf
[3]http://www.scienceticker.info/news/EplFkFZylueYfhTGPv.shtml